Automated Equipment Safety Inspection Verification: A Smarter Process with AI Agents for Equipment Managers
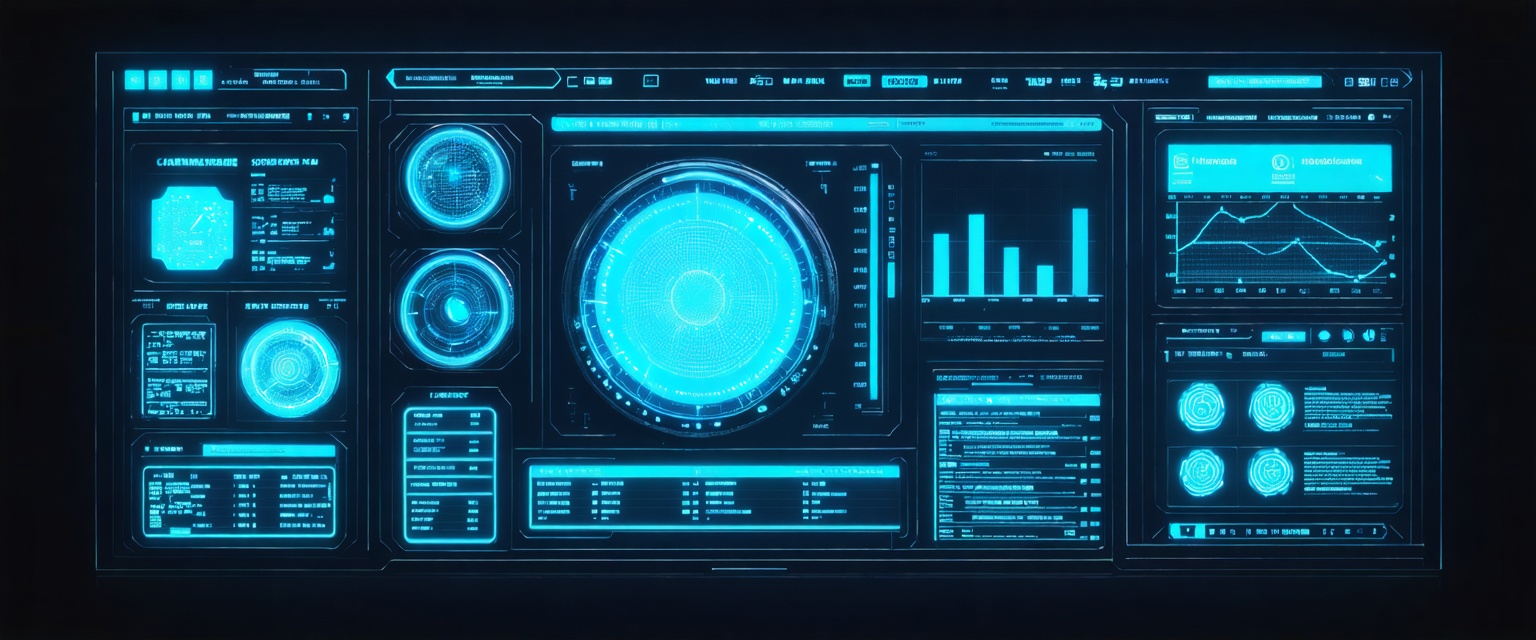
Revolutionize equipment safety verification. Learn how AI agents automate inspections, slash manual processing, and enhance safety protocols efficiently.
Keeping up with safety inspections shouldn't mean drowning in spreadsheets, emails, and missed follow-ups. But for equipment managers, outdated verification methods create delays, inconsistent records, and unsafe blind spots.
Agentic AI is changing that. AI agents now automate inspection verification, flag risks faster, and help enforce consistent safety protocols.
Datagrid’s data connectors make it easier than ever to plug this AI into your existing tools. This article breaks down how AI agents streamline safety inspections without overhauling your systems.
What Equipment Safety Inspection Verification Entails
Equipment safety inspection verification is the systematic process of confirming that machinery and tools meet established safety standards and regulatory requirements. This critical workflow involves selecting equipment for review, performing comprehensive safety checks, documenting findings, and verifying that corrections have been properly implemented.
The Need for Automated Equipment Safety Inspection Verification
The industrial world demands tougher verification than ever. Regulatory bodies have tightened requirements across industries, while equipment complexity has increased significantly.
Poor equipment inspections lead to thousands of workplace injuries every year, with violation fines reaching substantial amounts.
A missed safety hazard in manufacturing can idle production lines for days. Equipment failures in healthcare facilities put patients at risk.
Construction sites with faulty machinery face not just accidents but project delays and contract penalties.
Who Handles Inspection Verification and What's at Stake?
Equipment managers, safety supervisors, and compliance officers bear the burden of inspection verification. They're your first defense against equipment disasters.
For equipment managers, everything's on the line. Beyond keeping people safe, they face potential legal troubles, regulatory penalties, and the fallout from equipment failures.
When verification processes fail, the consequences extend beyond immediate incidents. Healthcare facilities have faced lawsuits when medical equipment malfunctions harmed patients.
Manufacturing plants have experienced catastrophic failures that traced back to inadequate inspection verification protocols.
Why Equipment Managers Need Rigorous Safety Inspection Verification
Safety isn't just a checkbox, it's your operation's backbone. Solid inspection verification keeps your team safe, keeps operations running, and controls costs in complex industrial environments.
Protecting Lives and Assets
Above all, thorough safety inspections save lives. By verifying equipment meets safety standards, you dramatically cut accident risks. This isn't about ticking boxes, it's about everyone going home safely after their shift.
The benefits go beyond human safety. Good verification protects your equipment investment.
Regular, thorough inspections catch small problems before they become disasters, extending machine life and reducing unexpected downtime.
Justifying Budgets and Decisions
As an equipment manager, you constantly defend maintenance budgets and purchasing choices. Solid inspection verification gives you the ammunition you need.
Detailed inspection records show why preventative maintenance matters.
Trends from verified inspections backup equipment replacement plans.
Compliance reports based on thorough verification shield against liability claims.
This data-driven approach builds credibility with management and stakeholders.
The Real Costs of Poor Verification
Skip rigorous safety inspection verification and you'll pay the price:
- Unexpected Equipment Failures: Poor verification misses warning signs, leading to breakdowns and production stops.
- Regulatory Fines: Weak safety documentation can trigger massive penalties, potentially costing significant amounts.
- Injuries and Lost Productivity: When safety measures aren't verified properly, workplace accidents spike, causing injuries, downtime, and dropping morale.
- Reputational Damage: Safety incidents can damage your organization's reputation, hurting customer relationships and recruiting efforts.
The Friction Points in Safety Inspection Verification Workflows
Despite its critical importance, safety inspection verification often gets bogged down by inefficiencies that compromise workplace safety and operations.
Manual Data Entry and Documentation Bottlenecks
One major headache is reliance on manual data entry and paper forms. This approach wastes time and invites errors.
Manual safety processes create isolated data islands, making it hard to see the complete safety picture.
Manual data entry problems include scattered documentation across fragmented storage systems, high error rates, and limited historical analysis due to data spread across different systems.
These issues mean critical information gets missed during inspections and recurring problems go unnoticed.
Inconsistent Inspection Processes
Another pain point is quality variation and lack of standardized workflows. This inconsistency creates overlooked inspection points, skipped verification steps, and unreliable hazard detection.
Narrow safety inspection approaches can lead to serious accidents. Workers can be injured by machinery despite "comprehensive" safety documentation.
This highlights why thorough, consistent inspection processes matter.
Delays in Corrective Action and Communication
Slow reporting and fragmented communication between inspectors, equipment managers, and maintenance teams delay hazard fixes. This shows up as slow transmission of findings to key people.
There's often no real-time visibility into equipment status and poor resource allocation for fixing identified hazards.
These delays put safety at risk and hurt operational efficiency. Equipment managers struggle to make timely decisions because they lack current information.
How AI Agents Automate Equipment Safety Inspection Verification
AI agents are reshaping equipment safety inspection verification through smart technologies that boost accuracy, consistency, and efficiency for equipment managers. These AI-driven improvements are being adopted across industries, enhancing safety protocols and inspection verification processes, particularly in AI in construction safety.
Real-Time Data Capture and Automated Checklists
AI agents walk inspectors through interactive, dynamic checklists that ensure complete inspection steps and accurate real-time data capture. Unlike static paper forms, these smart systems adapt to specific inspection contexts.
AI-powered platforms have eliminated manual data entry, cut transcription errors, and created more reliable safety data trails.
This automation enables instant safety monitoring across multiple sites, cutting inspection workload while improving overall site safety.
AI-Powered Hazard Detection and Verification
AI excels at analyzing images and sensor data to automatically flag hazards, rate their severity, and suggest fixes. This capability far outstrips human attention to detail and consistency.
Computer vision systems in manufacturing continuously monitor factory floors, analyzing video feeds for problems like oil leaks, unauthorized access, or equipment issues.
These systems catch subtle hazards that human inspectors might miss, leading to faster fixes and fewer accidents.
Streamlined Documentation and Compliance Reporting
AI agents create, organize, and store inspection records in real-time, supporting immediate regulatory compliance and audit readiness. This feature especially helps industries with strict requirements.
By centralizing and digitizing compliance tracking, companies avoid fines and reduce regulatory risks.
Automated Alerts and Task Assignment
When hazards appear, AI agents trigger immediate notifications and assign follow-up tasks, ensuring quick response and accountability. This real-time AI notifications system is vital for maintaining a safe workplace.
Utilities companies use AI-powered helmet cameras and sensors to verify all personnel meet PPE requirements during inspections.
Alerts for non-compliance go straight to supervisors, improving both safety and audit readiness.
Continuous Improvement Through Data Analytics
AI agents gather inspection data over time, revealing patterns, recurring issues, and process improvement opportunities. This capability lets organizations take a proactive approach to safety management and process automation, even extending to areas like automating proposal creation.
Datagrid: AI-Powered Document Automation & Compliance for Construction
Construction professionals and equipment managers juggle an enormous volume of critical documents across projects. Datagrid's AI-powered platform turns this challenge into a strategic advantage.
By integrating with existing ERP systems and supporting CRM and DocuSign integration, Datagrid eliminates manual data entry, reduces errors, and creates a more trustworthy safety data trail.
Comprehensive Document Processing
Datagrid's AI analyzes thousands of construction documents at once, extracting key information without manual review. This cuts analysis time and reduces human error.
Automated Submittal Processing
AI agents in construction check material submittals against project specifications, flagging non-compliant items and tracking approval status across your document ecosystem.
This ensures all materials meet required standards, boosting project safety and quality.
Contract Compliance Monitoring
The platform extracts key obligations, deadlines, and requirements from contract documents, creating automatic alerts for upcoming deliverables and potential compliance issues.
This proactive approach prevents costly oversights and ensures all contractual safety requirements are met.
Inspection Documentation Management
Datagrid processes inspection reports across multiple projects and authorities, organizing findings, tracking resolution status, and identifying recurring issues.
This comprehensive view allows for more effective safety management and helps prioritize improvement areas.
Document Version Control
The system automatically identifies and compares document revisions, highlighting substantive changes between versions.
This ensures teams always work with current information, critical for maintaining up-to-date safety protocols.
Regulatory Documentation Validation
The AI verifies that project documentation meets jurisdiction-specific requirements for inspections, close-outs, and occupancy.
This reduces approval delays and compliance risks, ensuring smooth project progression.
Datagrid's AI-powered data connectors have revolutionized safety management for construction clients and equipment managers. By integrating with existing ERP systems, Datagrid eliminates manual data entry, reduces errors, and creates a more trustworthy safety data trail.
Simplify Equipment Safety Inspection Verification with Datagrid's AI
Don't let data complexity slow down your team. Datagrid's AI-powered platform is designed specifically for teams who want to:
- Automate tedious data tasks
- Reduce manual processing time
- Gain actionable insights instantly
- Improve team productivity
See how Datagrid can help you increase process efficiency.
Create a free Datagrid account