Streamline MEP Coordination: How AI Agents Transform Utility Documentation
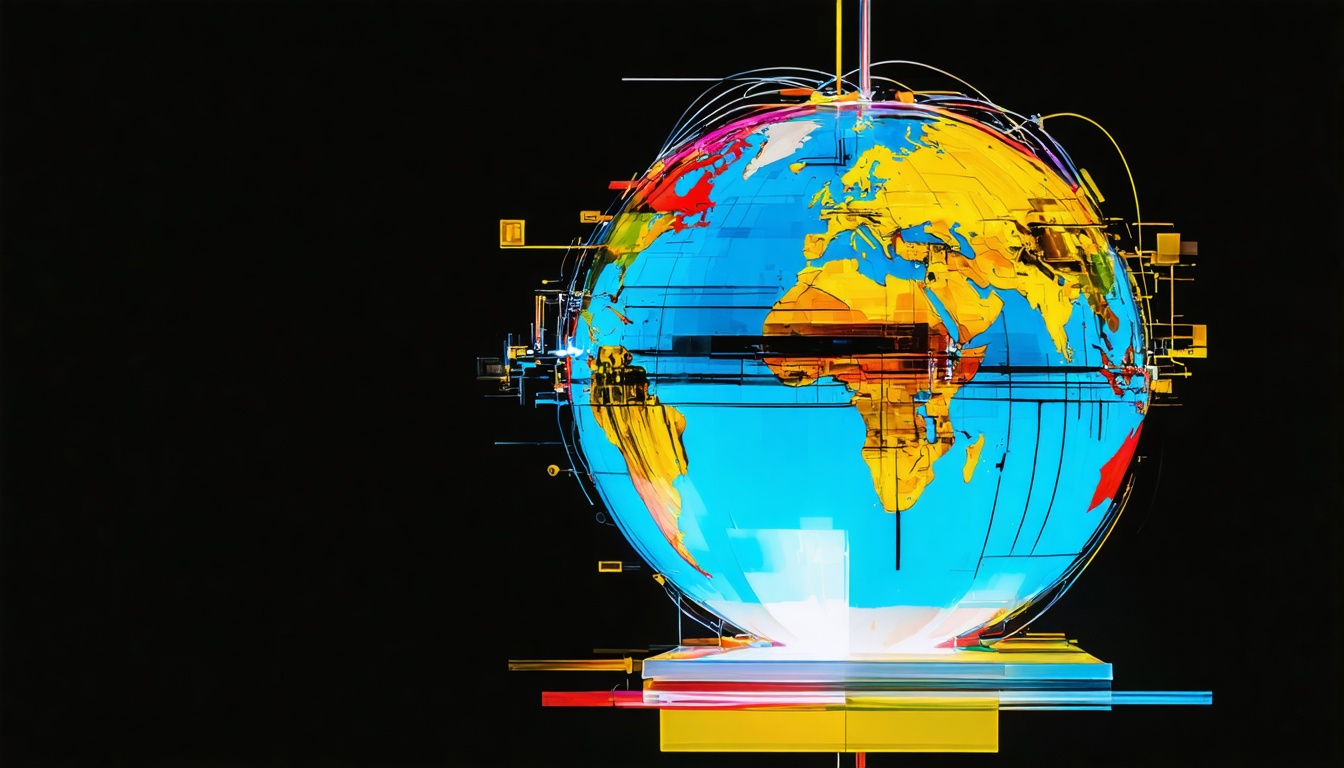
MEP coordinators spend 70% of their time processing data between disconnected systems—extracting clash coordinates from BIM models, cross-referencing utility specifications across project management platforms, and manually updating compliance matrices in spreadsheets.
This isn't coordination work; it's data entry that keeps you from the strategic problem-solving that projects actually need.
The cost of manual data processing hits hard. A single overlooked conduit route buried in email attachments can trigger days of rework, push back critical path activities, and inflate budgets that already run razor-thin. Unresolved clashes routinely cause project delays and costly change orders, especially when mechanical, electrical, and plumbing trades compete for the same ceiling space in tight urban footprints.
The real problem isn't your expertise—it's that utility coordination data still moves through email threads, spreadsheet trackers, and outdated PDFs. Every design revision forces another round of manual data extraction, version checking, and compliance cross-referencing.
Your team waits while you hunt through documents for the information they need to keep building.
AI agents eliminate this data processing bottleneck. Purpose-built agents ingest 3D models, extract clash coordinates automatically, generate relocation schedules from multiple data sources, and sync every stakeholder to real-time project data. Instead of you copying information between systems, AI agents handle data extraction, version reconciliation, and compliance verification—surfacing only the decisions that require human judgment.
Early adopters report 60% faster review cycles and 40% fewer field surprises because AI agents catch data inconsistencies before they become construction problems.
This guide shows you exactly how to deploy AI agents for utility coordination data processing, eliminate manual data work, and reclaim your time for actual project management. You'll also see how Datagrid's data connectors integrate models, schedules, and compliance records with your existing systems—no rip-and-replace required.
What is Utility-Coordination Documentation?
Effective utility-coordination documentation captures the spatial puzzle of MEP systems competing for the same ceiling space. It includes detailed system layouts from 3D models, installation schedules with sequencing and labor windows, material specifications, and clash-detection reports that flag spatial conflicts.
Platforms like Revizto's BIM workspace generate clash reports automatically, and even when the source files live in BIM360 Docs, teams still spend hours processing the data into actionable project documentation.
Successful documentation requires four critical elements: accuracy because dimensions must reflect the latest design iteration, completeness so nothing from conduit fill percentages to vent terminations is left to guesswork, accessibility meaning every stakeholder can access current versions instantly rather than hunting through email threads, and traceability so you know who changed what and when during inspections or claims.
The documentation types span conflict matrices summarizing unresolved clashes, composite utility plans overlaying all trades, relocation schedules for existing services, and compliance reports proving code adherence.
Traditional methods involve overlaying drawings manually, swapping marked-up PDFs, and assembling revisions in shared drives—a slow, error-prone process that's difficult to audit when each trade works in isolation.
Because MEP systems are interdependent—shifting a duct may require rewiring a panel—coherent documentation becomes the only way to keep integrated systems moving together. As MEP coordination best practices demonstrate, rigorous documentation isn't paperwork; it's your primary defense against schedule overruns and budget creep caused by data processing bottlenecks.
Why Utility-Coordination Documentation is Important for MEP Teams
MEP coordinators process documentation from 15-30 different data sources daily—CAD files, specifications, clash reports, compliance matrices, installation schedules. This data fragmentation costs projects real money: spatial conflicts discovered during installation average $45,000 in rework per occurrence, and documentation errors cause 23% of MEP project delays.
Spatial conflicts hit first and hardest. Mechanical, electrical, and plumbing systems compete for ceiling space, and incomplete data integration means conflicts surface during installation instead of design. Teams spend 40 hours weekly processing clash detection reports across multiple platforms—Revit, AutoCAD, Navisworks, project management systems.
On commercial projects, coordination data processing consumes 6% of total MEP budget before installation begins. Every conflict caught through proper data integration saves $15,000 in field rework and prevents 3-day schedule delays.
Compliance verification creates another significant bottleneck. Building codes reference 200+ data points per system, and inspectors need audit trails proving code compliance through installation documentation. Manual compliance verification takes 12 hours per system review, and documentation gaps trigger re-inspections that cost $8,000 in crew demobilization. Integrated compliance data processing reduces verification time to 2 hours and creates audit trails that accelerate approvals by 65%.
Cross-discipline collaboration suffers most from data silos. Mechanical designers work from one data set, electrical teams from another, plumbing fabricators from spreadsheets maintained separately. Information gaps between these data sources create 18 coordination meetings per project phase, consuming 120 hours of team time.
When utility coordination data integrates across disciplines—clash reports, installation sequences, material specifications—teams resolve 80% of coordination issues through data analysis instead of meetings.
Modern MEP projects generate terabytes of coordination data across dozens of platforms. Manual data processing keeps experienced coordinators buried in document management instead of managing installations. Teams that automate utility coordination data workflows report 70% reduction in documentation time and 45% fewer field conflicts, freeing coordinators to focus on strategic project management instead of data entry.
Common Time Sinks When Creating Utility-Coordination Documentation
You already know the feeling: the schedule is slipping, subcontractors need answers, and you're still wrestling with paperwork instead of solving on-site problems. Every hour you pour into piecing together utility-coordination documents is an hour not spent optimizing layouts or de-risking the build. Four major inefficiencies consistently drain time from MEP teams.
Manual Clash Detection and Resolution
Finding spatial conflicts means overlaying plan sheets, toggling endless section views, and walking the model line by line. On complex jobs, mechanical ductwork, electrical conduits, and plumbing stacks compete for inches of ceiling space that simply don't exist in 2D. The hunt repeats every time an architect issues a revision, so you re-run the same checks, re-issue the same RFIs, and re-draft the same routing diagrams. Dedicated coordination efforts can swallow a significant slice of the MEP budget before a single hanger is installed. Tools like BIM-based clash detection exist precisely because the human-eye method is too slow and too error-prone to keep pace with design churn.
Document Fragmentation and Version Control
Even when clashes are ironed out, the documentation that proves it often lives everywhere—shared drives, personal desktops, cloud folders, or buried inside old email threads. One plumbing foreman is looking at "final_v7.pdf" while the electrical lead is marking up "FINAL_FINAL.dwg." Chasing the latest files, merging redlines, and archiving superseded sets can consume half a day before you touch any technical work. Version confusion also breeds costly mistakes: a single outdated riser diagram can ripple all the way to procurement and field installation. Smart document management shows how automating version tracking removes that bottleneck and gives every stakeholder one true source of information.
Cross-Discipline Communication Bottlenecks
Utility coordination succeeds only when mechanical, electrical, and plumbing teams see—and trust—the same data. In practice, that trust is built through marathon meetings, endless reply-all threads, and phone calls made from noisy job trailers. The administrative drag is real: you draft meeting minutes, log action items, and then translate verbal agreements back into formal documents so nothing is lost in transit. Misunderstand one dimension or overlook an agreed reroute, and you are back in the meeting room explaining why conduit now crosses a sprinkler main. The interdependency of MEP systems means poor hand-offs multiply quickly, turning simple questions into week-long coordination loops.
Compliance Verification and Reporting
Proving every coordinated layout meets code requires combing through local plumbing statutes, NEC clearances, energy standards, and owner specifications, then cross-referencing them against dozens of plan sheets. After that come the reports: annotated clash logs, stamped compliance checklists, and narrative justifications for inspectors. Each change order forces you to repeat the process to maintain an auditable trail.
Relying on manual look-ups invites human error and drains momentum right when construction is gearing up. AI-enabled compliance tools already embedded in modern construction workflows can flag violations automatically and regenerate updated reports in minutes—freeing you to focus on engineering decisions instead of paperwork. Similar automated claims processing insurance workflows prove that the same AI techniques can extract data from forms and accelerate approvals—exactly what construction documentation needs.
Marketing teams have already embraced automated branding to generate perfectly formatted proposal packages; construction projects can capture the same efficiency by automating utility documentation.
Every one of these time sinks chips away at your schedule and budget, but they share a common root: repetitive, documentation-heavy tasks that machines now handle better than humans. Eliminating them is the fastest way to reclaim your day and keep the build moving forward.
Datagrid: AI-Powered Document Automation & Compliance for Construction
Construction professionals manage an overwhelming volume of critical documents across projects, from contracts and submittals to inspections and certifications. Datagrid's AI-powered platform transforms construction document management:
Comprehensive Document Processing: Analyze thousands of construction documents simultaneously—contracts, specifications, submittals, RFIs, change orders, and compliance records—extracting key information without manual review.
Automated Submittal Processing: Deploy AI agents that automatically review material submittals against project specifications, identifying non-compliant items and tracking approval status across your document ecosystem.
Contract Compliance Monitoring: Extract key obligations, deadlines, and requirements from contract documents, creating automated alerts for upcoming deliverables and potential compliance issues.
Inspection Documentation Management: Process inspection reports across multiple projects and authorities, organizing findings, tracking resolution status, and identifying recurring inspection issues.
Document Version Control: Automatically identify and compare document revisions, highlighting substantive changes between versions and ensuring teams work with current information across the project lifecycle.
Permit and Certificate Tracking: Monitor expiration dates and requirements for permits, licenses, and certifications across projects, generating proactive alerts for renewals and compliance documentation.
Regulatory Documentation Validation: Verify that project documentation meets jurisdiction-specific requirements for inspections, close-outs, and occupancy, reducing approval delays and compliance risks.
By implementing Datagrid for document automation and compliance, your construction team can eliminate time-consuming document reviews, reduce compliance risks, and ensure critical information flows seamlessly between stakeholders—transforming document management from a burden into a strategic advantage.
Simplify construction tasks with Datagrid's Agentic AI
Don't let data complexity slow down your team. Datagrid's AI-powered platform is designed specifically for teams who want to:
- Automate tedious data tasks
- Reduce manual processing time
- Gain actionable insights instantly
- Improve team productivity See how Datagrid can help you increase process efficiency.