Maximize Quality Assurance in Manufacturing: How AI Agents Automate Deviation Detection
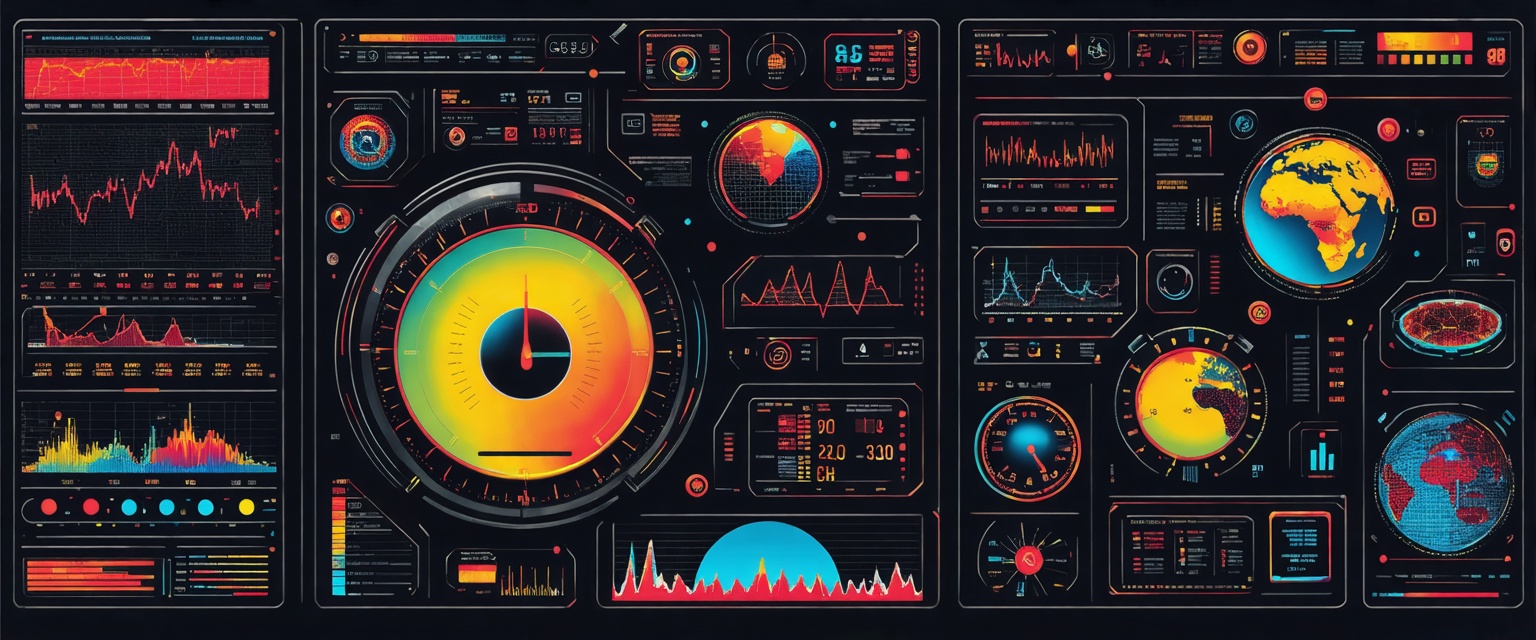
Maximize Quality Assurance in Manufacturing: How AI Agents Automate Deviation Detection
Manual methods of detecting process deviations often miss early signs of failure, especially when relying on periodic checks or human observation. Subtle anomalies slip through, leading to waste, rework, and compliance issues that strain quality assurance teams.
Thanks to advancements in Agentic AI, AI systems now continuously analyze production data to catch deviations early, before they turn into costly problems.
Datagrid’s AI agents take on this task automatically, spotting patterns and raising alerts faster than manual reviews.
This article explains how AI agents automate manufacturing process deviation detection for quality assurance directors.
Understanding Process Deviation Detection
Process deviations are measurable mismatches between expected production targets and actual parameters. These include temperature fluctuations, pressure variations, speed changes, or quality metrics that drift outside established ranges.
Critical deviations threaten safety, compliance, or product quality directly. Examples include pressure levels exceeding safety limits or contamination events that compromise entire batches.
Non-critical deviations impact performance and efficiency without immediate product integrity risks. These might include slight cycle time delays or minor temperature variations within acceptable bounds.
Production data contains early warning signals, subtle patterns indicating drift before parameters become problematic. Catching these signals allows intervention earlier, maintaining tighter control and preventing quality issues rather than addressing consequences afterward. By leveraging AI to enhance operational efficiency, manufacturers can detect these deviations promptly.
The Role of Deviation Detection in Driving Quality Assurance Efficiency
Deviation detection shapes product consistency, operational costs, and regulatory standing. For quality assurance directors, real-time detection systems prevent defects instead of managing their aftermath.
Real-time monitoring in manufacturing substantially reduces defect rates in automotive manufacturing. It represents the difference between continuous monitoring and periodic inspections, catching variances immediately rather than hours or days later.
The cost impact affects the bottom line quickly. Proactive detection reduces waste while improving first-pass yield rates. Catching a temperature spike in a chemical process early saves entire batches, preventing rework, scrap, and delayed shipments.
Critical deviations affecting safety, compliance, or product integrity need instant response. Non-critical deviations affecting efficiency can be addressed systematically.
Tracking both types builds a quality framework that handles immediate threats while optimizing long-term performance.
Deviation data becomes a roadmap for improvement. Modern quality systems use deviation patterns to identify recurring weak points, enabling targeted fixes that address root causes rather than symptoms.
This shifts operations from putting out fires to strategic quality enhancement.
For regulated industries, deviation records form the backbone of compliance documentation. Pharmaceutical operations must document and investigate all deviations under Good Manufacturing Practice requirements.
Accurate detection ensures quality records meet regulatory standards while providing audit-ready traceability.
The Inefficiencies of Manual Deviation Detection in Quality Assurance
Manufacturing quality control requires rapid identification of process deviations, but manual detection methods create significant vulnerabilities.
As production complexity increases and data volumes grow, human-centered approaches fail to maintain consistent quality standards, leaving manufacturers exposed to escalating quality risks and compliance failures.
Time-Consuming and Prone to Oversight
Manual deviation detection forces quality teams into a reactive position where issues are discovered only after production completes. This approach introduces critical delays between when problems occur and when they're identified.
Human capabilities have natural limitations when processing large datasets without systematic support. Quality staff can miss subtle parameter mismatches when monitoring multiple variables simultaneously.
Critical deviations slip through when they manifest as gradual shifts rather than obvious spikes, allowing problems to progress undetected until they become severe quality incidents.
Inconsistent Interpretation and Response
Different team members often interpret the same deviation data differently. What one operator considers minor, another may flag as significant, creating inconsistent quality responses across your operations.
Human factors contribute significantly to process deviations, including variations in training levels and attention to detail. These differences make it impossible to establish uniform quality standards or consistent deviation handling protocols.
Limited Scalability and Resource Drain
Manual detection methods collapse under the weight of increasing complexity. As production scales up, the volume of parameters requiring monitoring grows exponentially, quickly overwhelming quality teams.
The resource drain intensifies when skilled personnel spend their time reviewing routine data instead of addressing root causes or improving processes.
Adding more manual reviewers to compensate for increased production volume creates additional coordination challenges and introduces more variability into quality decisions.
Delayed Visibility and Missed Trends
Manual approaches excel at identifying isolated incidents but fail dramatically at spotting patterns across time periods or production batches. Without systematic trend analysis, quality teams remain blind to recurring issues.
This limitation prevents recognition when seemingly minor deviations actually indicate larger systemic problems developing within production processes.
When patterns remain invisible to manual review, process deviations keep recurring because their underlying causes go unaddressed. This reactive approach undermines proactive quality improvement efforts and leaves manufacturers vulnerable to quality degradation over time.
How AI Agents Automate Manufacturing Process Deviation Detection
Manufacturing operations generate massive volumes of process data that human monitoring alone cannot effectively analyze. AI agents transform deviation detection by continuously monitoring production parameters across complex manufacturing environments, identifying subtle variations before they impact quality or efficiency.
Real-Time Monitoring Across Complex Data Streams
AI agents ingest continuous process data and compare it against established baselines in real time. They adapt to normal process variability and identify subtle deviations that signal emerging issues.
Vision systems catch microscopic imperfections and alignment variations that human inspectors might miss, particularly with customized products. This real-time evaluation gives manufacturers tighter control of both quality and efficiency.
Early Pattern Recognition and Predictive Insights
AI agents spot trouble before it happens by detecting small anomalies and patterns that precede process failures. Advanced models anticipate equipment issues and reduce unplanned downtime through proactive maintenance recommendations.
By leveraging AI to automate complex analysis, manufacturers can shift from reactive to predictive detection, cutting waste, downtime, and rework costs while boosting production reliability. Additionally, proactive data handling with AI enables early intervention before minor issues escalate.
Context-Aware Decision Making
AI agents don't just flag out-of-range values; they interpret deviations within operational context. A pressure spike during equipment startup is normal; the same spike during steady operation signals trouble.
Contextual intelligence allows systems to identify faulty items and recommend specific adjustments based on operational conditions. This smart interpretation reduces false alarms and helps quality teams focus on genuine problems.
Scalability Across Lines and Facilities
AI agents deploy consistently across multiple production lines and facilities, delivering standardized deviation detection at scale. As operations grow complex, AI systems maintain performance without requiring more quality staff.
Deviation detection technology reduces defect rates and waste while maintaining consistent quality standards, delivering results that scale across global operations.
Datagrid for Manufacturing Professionals
Your production data, supply chain documentation, and quality control information live in different systems, making insights nearly impossible to get when you need them. Datagrid’s AI platform handles the document processing and data analysis that typically slows down manufacturing teams.
The platform allows teams to focus on production innovation while AI handles document-heavy work that creates operational bottlenecks. Let's explore key applications:
Supply Chain Documentation Management
Process thousands of supplier specs, BOMs, and compliance certificates at once. Extract critical information to maintain visibility across your supply network without the manual bottlenecks that slow down purchasing pattern analysis and supplier qualification. By automating data processing in manufacturing, you can streamline operations and reduce errors.
Quality Control Automation
Stop chasing production data, testing reports, and defect documentation across multiple systems. AI agents analyze this information to spot patterns, predict quality issues, and generate improvement recommendations before problems escalate. This is how AI optimizes complex workflows in manufacturing environments.
Regulatory Compliance Support
Keep up with changing ISO, FDA, and EPA requirements without drowning in paperwork. AI agents monitor regulation changes and cross-reference your docs to flag compliance gaps, reducing audit risks and costly failures. By streamlining manufacturing documentation and automating safety documentation, you can ensure compliance effortlessly. Additionally, AI in automating manufacturing reporting helps maintain regulatory standards.
Equipment Maintenance Optimization
Your maintenance logs and equipment manuals contain insights that prevent costly downtime. Extract these insights to predict maintenance needs and shift from reactive repairs to predictive strategies that extend asset lifecycles. By optimizing manufacturing processes with AI, you can enhance equipment performance and longevity.
Production Workflow Analysis
Managing multiple facilities means processing production reports from diverse locations and systems. Datagrid analyzes this data to identify bottlenecks and best practices you can implement across your organization. By automating data handling in manufacturing and optimizing manufacturing workflows, you can improve efficiency across all sites.
Product Specification Management
Technical specs scattered across document formats create information silos that slow decisions. Automatically extract and organize these specifications for quick comparisons between design requirements and production capabilities, accelerating product development and change management.
Supplier Performance Evaluation
Stop manually reviewing vendor documentation, delivery records, and quality reports from multiple sources. Generate comprehensive supplier scorecards and identify strategic sourcing opportunities with data-driven insights for relationship management. Utilize AI-powered data integration for seamless supplier assessments. Also, the automation of manufacturing documentation enhances supplier communication and performance tracking.
Simplify Manufacturing Tasks with Datagrid's Agentic AI
Don't let data complexity slow down your team. Datagrid's AI-powered platform is designed specifically for teams who want to:
- Automate tedious tasks in manufacturing
- Reduce manual processing time
- Gain actionable insights instantly
- Improve team productivity
See how Datagrid can help you increase process efficiency.