Revolutionize Your Manufacturing Operations: How AI Agents Automate Bottleneck Identification for Operations Directors
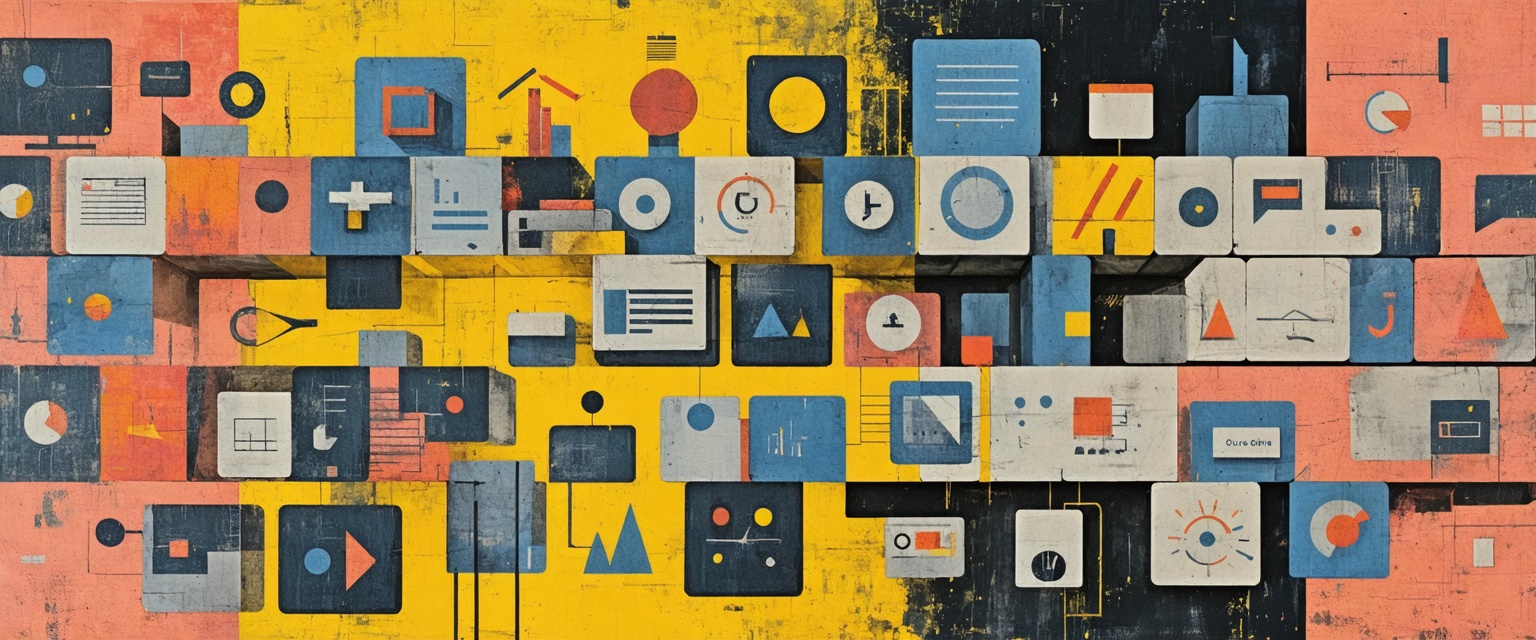
Discover how AI agents automate bottleneck identification in manufacturing for Operations Directors, boosting productivity & streamlining operations effectively.
Fragmented data across disconnected manufacturing systems makes it difficult for operations directors to identify bottlenecks before they disrupt output. This hidden inefficiency quietly drains productivity and delays decision-making.
Thanks to advancements in Agentic AI, it’s now easier than ever to unify these data sources and surface constraints automatically.
Datagrid’s data connectors pull from multiple systems in real time, giving AI agents the complete picture they need to detect issues early.
This article explores how AI agents automate manufacturing operational bottleneck identification for operations directors.
Understanding Manufacturing Operational Bottleneck Identification
A bottleneck in manufacturing is any process, machine, or workflow stage that constrains the overall production capacity. This creates a cascade of delays and inefficiencies throughout the system. In modern manufacturing environments, operational bottlenecks can emerge from multiple sources, making them particularly challenging to identify and resolve.
The various types of manufacturing operational bottlenecks are:
- Equipment Bottlenecks: Caused by outdated or unreliable machines that slow down production. Often requires major investment to fix.
- Process Bottlenecks: Result from workflow inefficiencies like long wait times or slow changeovers. Monitoring queues helps spot them early.
- Material Bottlenecks: Occur when delays or quality issues in raw materials disrupt flow. Strong inventory systems help prevent these.
- Labor Bottlenecks: Stem from workforce issues such as absenteeism or skill gaps. They especially impact specialized tasks.
The impact of operational bottlenecks extends throughout manufacturing operations:
- Reduced throughput limits production well below theoretical capacity
- Increased costs from idle workers and equipment waiting on constrained processes
- Quality issues when delays cause material spoilage or damage
- Extended lead times that frustrate customers and threaten business relationships
- Decreased flexibility to adapt to demand fluctuations or product changes
Given this complexity, systematic bottleneck identification is essential. This requires continuous monitoring of production metrics, regular analysis of process flows, and implementation of advanced analytics tools for real-time detection.
Why Effective Bottleneck Management is Key for Operations Directors
Your success as an operations director comes down to optimizing production flow and driving growth. Bottleneck management directly impacts your key performance metrics.
Think of bottlenecks as traffic jams in your manufacturing system. They cap your output below what your plant can actually produce, making it tough to hit targets and meet customer needs.
These constraints waste money through idle resources and underused equipment.
When bottlenecks cause delays, your lead times stretch out—and customers might start looking at more reliable competitors. In manufacturing, delivery reliability can be your biggest strength or fatal weakness.
Quality takes a hit when processes get strained. Bottlenecks increase errors and defects, creating waste, rework, and potential reputation damage if bad products reach customers.
Most critically, bottlenecks kill your ability to adapt. When you can't quickly adjust to changing demand or product requirements, you miss market opportunities.
By tackling manufacturing operational bottlenecks proactively, you can:
- Boost overall throughput and productivity
- Cut operational costs and improve resource utilization
- Enhance product quality and consistency
- Improve customer satisfaction through faster delivery
- Increase operational flexibility and market responsiveness
Your bottleneck management skill separates manufacturing operations that merely survive from those that thrive. It's about building continuous improvement into every aspect of operations.
How Manual Bottleneck Identification Wastes Time
Identifying production bottlenecks is crucial for optimization, but traditional methods often lead to significant time waste. Here are the most common time traps that slow down effective bottleneck detection and resolution.
Manual Data Collection
Walking the production floor with clipboards or manually entering data into spreadsheets introduces errors and prevents real-time visibility into equipment performance. If a production line goes down unexpectedly, operators might not record the downtime until hours later.
This delay hampers both response and root cause investigation. Manual data collection keeps teams constantly playing catch-up rather than proactively addressing emerging bottlenecks.
Delayed Reporting
When performance data isn't available until shift end or the next day, teams lose the opportunity to respond quickly to developing issues. A changeover consistently taking longer than planned might not be flagged until it has already affected multiple production runs.
These delayed insights prevent proactive adaptation, trapping teams in a reactive cycle of addressing problems after they've already caused significant disruption.
Reactive Problem-Solving
Without timely data or trend visibility, manufacturing operations often address bottlenecks only after major disruptions occur. For example, a packaging machine that jams several times weekly might only receive attention after causing complete shutdowns.
This reactive approach wastes time that could be saved through predictive maintenance or trend-based alerts, which would allow teams to address issues before they escalate into production-halting bottlenecks.
Siloed Information
Fragmented data across departments creates inefficiencies in bottleneck identification. When planning doesn't know a machine's lower throughput stems from overdue maintenance, or maintenance fixes issues actually caused by upstream scheduling errors, valuable time is wasted.
This lack of integration delays effective action as teams work with incomplete information or solve the wrong problems.
These time traps create compounding delays that severely impact manufacturing efficiency. Breaking free requires automated, real-time bottleneck detection systems that provide instant data collection, integrated reporting across departments, and predictive analytics.
How AI Agents Automate Manufacturing Operational Bottleneck Identification
AI agents are transforming bottleneck detection, offering unprecedented speed and accuracy in optimizing production workflows for Operations Directors. The benefits of AI automation extend beyond detection, encompassing various aspects of manufacturing operations.
Core Technologies for Bottleneck Management
AI systems employ several key techniques to automate bottleneck identification:
- Machine Learning Models: Supervised learning algorithms analyze historical production data to predict bottlenecks based on past patterns. Unsupervised methods uncover hidden constraints in complex processes without requiring pre-labeled data.
- Digital Twins: These virtual replicas of factory operations enable continuous monitoring and simulation. AI models can experiment with changes virtually and pinpoint potential bottlenecks before they impact actual production.
- Predictive Analytics: By analyzing both historical and real-time data, predictive models forecast when and where bottlenecks will likely emerge, enabling proactive interventions before production slows.
- Process Mining: AI-driven process mining tools automatically extract insights from event logs, visualizing actual production flows and identifying recurring slowdowns.
Real-Time Bottleneck Detection and Resolution
AI agents excel at continuous production monitoring and rapid issue identification:
- Sensor Data Analysis: AI systems process data streams from IoT sensors and machines, immediately flagging deviations from normal operating conditions.
- Adaptive Process Control: Machine learning models dynamically adjust control parameters based on real-time analytics, eliminating bottlenecks caused by suboptimal settings.
- Root Cause Analysis: When bottlenecks are detected, AI uses pattern recognition and causal inference to identify underlying causes, enabling targeted fixes rather than generic troubleshooting.
Predictive Maintenance
One of AI's most valuable applications in bottleneck management is predictive maintenance. AI models forecast equipment malfunctions before they cause delays, scheduling maintenance just-in-time to prevent unplanned stoppages. This approach significantly reduces production bottlenecks caused by unexpected equipment failures.
By leveraging these AI techniques, operations directors can identify bottlenecks faster and more accurately while predicting and preventing them before they impact production. This proactive approach leads to smoother operations, reduced downtime, and improved productivity.
Datagrid for Manufacturing Professionals
As an operations director in manufacturing, you're constantly juggling production data, supply chain documentation, and quality control information across multiple systems. Datagrid's AI-powered platform streamlines these operations with specialized solutions:
Supply Chain Documentation Management
Process thousands of supplier specifications, bills of materials, and compliance certificates simultaneously. Our AI extracts critical information to maintain visibility across your entire supply network, reducing manual processing time and ensuring access to the latest data with document migration automation.
Quality Control Automation
Analyze production data, testing reports, and defect documentation to identify patterns and predict quality issues before they escalate. Datagrid generates targeted improvement recommendations through quality control automation, helping maintain high standards while reducing waste and rework.
Regulatory Compliance Support
AI agents continuously monitor changing industry regulations (ISO, FDA, EPA) and automatically cross-reference your documentation to identify compliance gaps. Stay ahead of regulatory requirements with our workflow automation guide and avoid costly non-compliance issues.
Equipment Maintenance Optimization
Extract insights from maintenance logs, equipment manuals, and performance data to predict maintenance needs, reduce downtime, and extend asset life cycles. Shift from reactive to predictive maintenance, maximizing equipment uptime and productivity.
Production Workflow Analysis
Process production reports across multiple facilities to identify bottlenecks, efficiency opportunities, and best practices for implementation throughout your organization. Streamline data collection, gain a holistic view of operations, and make data-driven decisions to optimize workflows.
Product Specification Management
Automatically extract and organize technical specifications from various document formats, enabling quick comparisons between design requirements and production capabilities. Ensure consistency across your product portfolio and streamline new product introductions.
Supplier Performance Evaluation
Analyze vendor documentation, delivery records, and quality reports to generate comprehensive supplier scorecards and enhance team communication, identifying strategic sourcing opportunities. Make informed decisions about supply chain partnerships based on data-driven insights.
By integrating Datagrid into your manufacturing operations, your team can focus on innovation and improvement while AI handles document-intensive tasks that typically create information silos and inefficiencies.
Simplify Manufacturing Tasks with Datagrid's Agentic AI
Don't let data complexity slow down your team. Datagrid's AI-powered platform is designed specifically for teams who want to:
- Automate tedious data tasks
- Reduce manual processing time
- Gain actionable insights instantly
- Improve team productivity
See how Datagrid can help you increase process efficiency.
Create a free Datagrid account.